ACOR
“Hemos reducido un 30% la huella hídrica en la planta gracias a la tecnología digital”
FRANCISCO MUÑOZ Director Planta Azucarera de ACOR
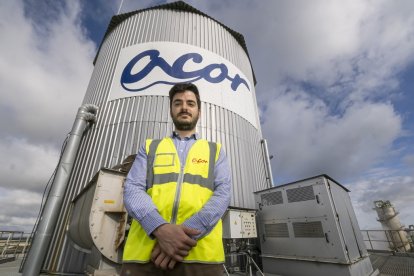
VALLADOLID. 13/06/23. PHOTOGENIC. PLANTA DE ACOR DEL OLMEDO, DIRECTOR DE LA PLANTA
Pregunta.– ¿Una industria puede ser sostenible y competitiva al mismo tiempo?
Respuesta.- Yo cambiaría la pregunta y me preguntaría si una industria puede ser insostenible y competitiva y la respuesta es no, con lo cual la sostenibilidad y la competitividad van de la mano y la clave es cómo se hace esa transición, no morir en el intento para llegar al equilibrio, pero a largo plazo yo no soy capaz de imaginar una industria que no sea sostenible y sea competitiva.
Pregunta.– ¿Qué impacto tiene la digitalización y la innovación realizada en la planta en la sostenibilidad? Respuesta.- El impacto es sustancial puesto que son medios, son ‘drivers’, la sostenibilidad es un fin en sí mismo, la digitalización y la innovación son medios mediante los cuales llegamos a distintos fines. En una industria madura como puede ser la azucarera, la innovación es compleja, es difícil, en un sector con 120 años de madurez, las oportunidades de mejora siempre aparecen con tecnologías disruptivas y ahora tecnologías digitales, con lo cual tienen un impacto sustancial porque son los únicos ‘drivers’ que nos permiten tener avances significativos en sostenibilidad. Acabamos de poner en marcha un proyecto para reducir el consumo de aceites, de motores, grasas, mantenimiento, generando órdenes de trabajo en automático gracias a la unión de la parte industrial y la parte de gestión del mantenimiento. Anteriormente, un operario realizaba el mantenimiento correctivo en un equipo en base a su experiencia o evidencia de avería y ahora se generan órdenes automáticas que las da el sistema de control por análisis de temperatura, consumo, vibración. También, gracias a la tecnología digital, hemos sido capaces de reducir la huella hídrica en un 30% En los últimos cuatro años en cualquier proyecto de mejora y eficiencia en la planta está presente la parte digital.
Pregunta.– ¿La Guerra de Ucrania ha obligado a replantearos la política energética de la planta azucarera?
Respuesta.- Aunque la respuesta es un poco contraintuitiva la respuesta es no. No ha ayudado a replantear porque desde antes de la guerra ya teníamos una hoja de ruta clara en materia de sostenibilidad, estaba dentro de nuestro Plan Estratégico y era un pilar fundamental y perfectamente definido. Es cierto que la guerra y el impacto socioeconómico y geopolítico ha ayudado a apuntalar y a evidenciar que esas líneas de trabajo eran las adecuadas.
Pregunta.– ¿Qué han modificado en los procesos industriales para no tener una dependencia tan alta del gas?
Respuesta.- Se puede separar en dos tipologías, una en la que se sustituye tecnología y otra en la que se mejora la eficiencia de un sistema o una instalación existente. En cuanto a la sustitución hemos modificado una parte del proceso en la que se utilizaban unos secaderos de gas natural para el secado de la pulpa, que se extrae de la remolacha una vez que se agota la sacarosa, se seca, se peletiza y se comercializa como alimentación ganadera. Ese secado se realizaba en secaderos de gas natural con un consumo exclusivo de gas natural y se ha sustituido por un secado solar que ha eliminado cualquier emisión de CO2 durante el proceso de secado, reduciendo el total de emisiones de la planta en un 33%. En cuanto a mejorar la eficiencia de la tecnología ya existente, hemos conseguido reducir el consumo de generación de vapor en un 15% a través de pequeñas modificaciones a nivel de ingeniería de procesos. Estamos trabajando para que los equipos existentes tengan el 100% de eficiencia según especificaciones de fabricante, modificando si hay alguna ineficiencia para que el equipo trabaje en condiciones óptimas.
Pregunta.– ¿Si el gas vuelve a los precios de antes de la guerra de la Ucrania, también se volvería a secar la pulpa con gas?
Respuesta.- No, porque los precios del gas del año pasado y del anterior nos han permitido realizar una amortización de la nueva planta de secado tan rápida que nos permite que los gastos futuros sean de operación, y teniendo en cuenta que los gastos de mantenimiento son prácticamente nulos y que solo tengamos gastos de operación. Esto implica que el precio de equilibrio que justificaría el volver a trabajar con gas natural sea un precio sustancialmente inferior al que teníamos antes de la guerra.
Pregunta.– ACOR y ENSO trabajan en la puesta en marcha en próximas fechas de una de las plantas de Cogeneración de Biomasa más grandes de España. ¿Qué ventajas tiene esa planta respecto a la situación actual?
Respuesta.- Esta planta va a tener dos beneficios: a corto plazo, la eliminación de todas las emisiones de CO2, con lo cual pasamos a tener cero emisiones en toda la generación de vapor. A medio y largo plazo nos permite un beneficio potencial de utilizar distintas biomasas agrícolas que a día de hoy no tienen porque estar encima de la mesa. Permite esta nueva vía de explotación de nuevos combustibles, así como generación de fertilizantes a partir de las cenizas de la combustión, es una nueva vía de investigación que con la tecnología actual no tiene cabida.
Pregunta.– El ahorro de agua, tanto en el campo como el proceso industrial es uno de retos de la industria agroalimentaria. ¿Qué medidas han tomado para reducir el consumo hídrico?
Respuesta.- Hemos intentado emprender distintas iniciativas para reducir el consumo, con una reducción de un 30% respecto a las campañas anteriores, o en términos absolutos 300.000 metros cúbicos de ahorro de consumo de agua gracias a la tecnología. Emprendimos un proyecto de monitorización, para conocer los puntos clave del consumo y tener la evidencia exacta. Se hizo un despliegue de varios sensores en distintos puntos para conocer cuánta agua estamos consumiendo en las fases del proceso. A raíz de ese conocimiento emprendimos actuaciones que nos permitiesen reducir el consumo en los distintos puntos que estábamos midiendo. Particularmente, reutilizando agua de distintas fases del proceso que tiene calidad suficiente para poderse utilizar e implicar una no reposición de agua limpia.
Pregunta.– Este año estrenaron el punto 0 de recepción de remolacha. ¿Qué balance hace de su primera campaña?
Respuesta.- El balance ha sido excepcional, mejor de lo que éramos capaces de cuantificar antes de ejecutar el proyecto. Toda la parte tangible de ahorro se materializó de forma directa, fue una puesta en marcha sin grandes problemas, no cometimos ningún error en las estimaciones que hicimos respecto a la parte intangible, esos beneficios potenciales que no éramos capaces de cuantificar, nos han dado bastantes sorpresas porque nos han permitido reducir de una manera muy importante distintos consumos de tratamiento de agua. Hemos reducido a la mitad todo el lodo de depuración realizando una separación de tierra en seco sin que entre en contacto con el agua. Hemos reducido mantenimiento, consumo eléctrico, térmico, y simplificando la operativa. En la reducción del 30% de huella hídrica, el punto 0 representa el 10%.
Pregunta.– ¿Esta planta que usted dirige podría trabajar solo con energías renovables? ¿La planta podría trabajar con placas fotovoltaicas?
Respuesta.- Esta planta puede trabajar con energías renovables y va a trabajar solo con ellas en el medio plazo. Una vez que el proyecto de biomasa esté en marcha quedarán pequeños detalles para conseguir esa independencia de los combustibles fósiles. La planta no puede trabajar con energía fotovoltaica porque no podemos olvidar que es una generación coyuntural, depende siempre de la presencia y la intensidad del sol. Una planta con demanda estable como puede ser nuestro proceso, que trabajamos 24/7 no puede depender de una fuente variable. No es una solución, pero sí un buen complemento. En Acor no pensamos que exista una solución única en cuanto a alternativa de tecnología energética, sino un mix para no depender de los combustibles fósiles. En el perfil de consumo tiene cierta importancia la parte fotovoltaica en el periodo de no actividad, es cuando más aporta porque el perfil de consumo sí coincide con las horas de sol y más generación eléctrica y hay un ‘match’ perfecto entre la oferta y la demanda.
Pregunta.– Ahora que se habla mucho de arraigo al territorio, ¿qué importancia tiene esta zona que se asienta Acor en el desarrollo del su negocio?
Respuesta.- El territorio aporta a Acor tanto como Acor aporta al territorio, por la propia naturaleza de la empresa, el estar presente en el medio rural es un mensaje claro y directo, tenemos el origen en el campo y queremos cerrar aquí el círculo económico y la generación de valor. Nuestro ciclo económico comienza con una semilla en el medio rural y tenemos que conseguir que termine en el mismo punto. Estamos orgullosos de tener la presencia y el impacto que tenemos en el ámbito rural y nos ayuda a que los trabajadores de la planta, al ser una empresa que aporta calidad en el puesto de trabajo, nos cataloguen como una empresa atractiva. Esto implica que el compromiso medio del trabajador sea más intenso al que podíamos tener si estuviéramos más cerca de un núcleo más grande como Valladolid.
“Entendemos la economía circular en toda la cadena productiva”
Javier Areños Director Planta de Tratamientos de Aceites y Oleaginosas de ACOR
Pregunta.– ¿La economía circular de una explotación agraria puede trasladarse a una industria agroalimentaria?
Respuesta.- Sí, la economía circular debemos entenderla dentro de la cadena productiva, desde la obtención de las materias primas, las semillas oleaginosas hasta el producto final que destinamos a los clientes que es el aceite para uso humano. En el caso de Acor tenemos el control de todo el proceso, nuestros socios son agricultores y como tal en las explotaciones agrarias se hace un control de toda la gestión del campo y se encuentran apoyados por el servicio agronómico de Acor y se hace un control exhaustivo de la dosis de siembra, de abonados, los productos fitosanitarios y las dosis de riego, y forma parte de esa economía circular y de la sostenibilidad. Tenemos además la parte industrial con la transformación de esos productos agrarios de una manera sostenible y respetuosa con el medioambiente y los recursos naturales.
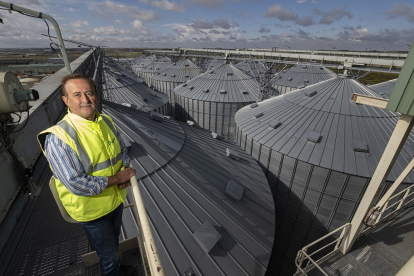
Javier Areños Director Planta de Tratamientos de Aceites y Oleaginosas de ACOR
Pregunta.– ¿Qué procesos de la planta entran en esa esa economía circular? Respuesta.- La planta es un proceso integral. Son diferentes partes de un proceso que se van ejecutando de una manera continuada y lo que está incluido en esa sostenibilidad es el proceso integral. Esta planta nació en sus orígenes para la obtención de biodiesel y tenemos la certificación internacional de sostenibilidad y carbono (ISCC) que nos permite garantizar la sostenibilidad de nuestros productos cuando van a usos energéticos. En este momento con la colaboración de nuestros socios de Agropro estamos ampliando este proceso y estamos en disposición, a partir de los socios, de ofrecer esa sostenibilidad al sector alimentario. Hay muchos clientes que están demandando ya que los productos que retiran de nuestras instalaciones tengan una certificación de sostenibilidad y estamos en disposición de facilitarles esas certificaciones.
Pregunta.– ¿Cuál es el destino de los subproductos?
Respuesta.- La instalación tiene como objetivo principal la producción de aceite refinado para uso alimentario, este sería el producto principal, pero bien es cierto que a lo largo de todo ese proceso industrial se producen otros coproductos que van saliendo a lo largo del proceso. Uno de ellos son las harinas que se dedican a alimentación y principalmente nuestros clientes son fábricas de pienso que hacen diferentes formulaciones. Y luego en el proceso más propiamente del refinado de los aceites hay dos coproductos como son los destilados del aceite y las pastas, que se obtienen de la neutralización y de la eliminación de fósforo. Estos dos productos se comercializan a través de diferentes empresas en una reutilización para actividades industriales.
Pregunta.– ¿Cómo gestionan los residuos generados en la fábrica?
Respuesta.- Todos los residuos que se generan se tratan a través de un gestor autorizado. Tenemos el compromiso con el gestor con el que trabajamos que más del 98% de los residuos generados se pueden reutilizar y no van como residuos finales. Por un lado intentamos ajustar al máximo las condiciones del proceso para añadir menos reactivos y generar menos residuos en la parte industrial y una segunda pata de esa labor es el incremento del mantenimiento predictivo, quiere decir que hacemos más mantenimiento predictivo y menos correctivo y preventivo. Lo que motiva es que alargamos la vida útil de los componentes que tenemos, aceites para reductores, piezas de cambio, hacemos un análisis para ver si podemos estirar su vida útil.
Pregunta.– ¿Qué proyectos están estudiando para disminuir los consumos energéticos y los residuos? Respuesta.- Estamos trabajando en dos proyectos: uno de ellos es la instalación de un economizador en una caldera convencional, es un equipo que anterior a la Guerra de Ucrania apenas se utilizaba y cada vez más por las circunstancias está teniendo más protagonismo y estamos evaluando esa posibilidad para reducir el consumo de combustibles fósiles, gas o gasoil, en cada momento que estemos trabajando con uno u otro combustible. Tenemos un segundo proyecto que es el análisis de la posibilidad de utilizar internamente unas tierras que se utilizan en el proceso del refino y que se están tramitando a través del gestor autorizado. Estamos valorando utilizarlas dentro de la fábrica.
Pregunta.– ¿Se puede ahorrar agua en el proceso industrial?
Respuesta.- Se puede y se debe ahorrar agua. Hay dos líneas básicas del Plan Estratégico de ACOR como son la reducción de la huella hídrica y la reducción de las emisiones de CO2 o la llamada descarbonización. Para la disminución del carbono estamos ajustando los consumos en planta. Hay que tener en cuenta que hay medidas que afectan a las dos líneas. Un ahorro en el consumo de vapor ayuda a la descarbonización y también a reducir la huella hídrica, no deja de ser agua en estado gaseoso. En cuanto a la reducción de la huella hídrica lo hacemos además en el tratamiento de las aguas que aportamos a la torre de refrigeración para mejorar esa calidad y reducir la cantidad de agua que tenemos que aportar a la torre para mantenerla en equilibrio y que las purgas de este equipo sean menores y se reduce el consumo. Otra línea en la reutilización de aguas es que estamos dando otro uso a las aguas de purga o las de lluvia, almacenando en una balsa y esas aguas las estamos utilizando para riego u otros usos.
Pregunta.– ¿Cómo ha afectado la Guerra de Ucrania al día a día de la fábrica?
Respuesta.- Nos ha hecho cambiar a todos y adaptarnos a las nuevas circunstancias siendo muy flexibles pero también ágiles. Diariamente analizamos los costes de la energía, del gas, del gasóleo, de la electricidad para modificar nuestro sistema de producción. Ucrania y Rusia son de los mayores productores a nivel europeo de semillas oleaginosas, principalmente girasol, y ha provocado una evolución de los precios incontrolada. La mayor parte del producto es nacional y de Castilla y León y hemos podido suministrar todos los contratos de los clientes.